
Everything You Need to Know about 3D Printing with SLA
When 3D printing with SLA, you can obtain high-quality prints with laser-precise details. Want to dive into the world of resin printing but don’t know where to start? This guide covers all the essentials of 3D printing with SLA.
What is SLA?
Stereolithography (SLA) is a vat polymerization printing method by which resin is heated using a focused laser. SLA resin must be UV-sensitive to allow the laser to cure specific areas of resin to build the part.
Charles Hull pioneered this technology, which was later patented in 1986. The ability to cure resin according to a program paved the way for the kinds of extremely detailed prints we have seen today in both hobby and industrial applications from tabletop figurines to medical models.
SLA is different from the more-common Fused Deposition Modeling (FDM) 3D printing technology, which lays heated filament layer-wise. SLA stands apart not only in its printing method but also because it allows for incredibly high-resolution printing. This style is perfect for minuscule details, such as those for delicate miniatures, as SLA prints can have layers under 50 microns thick.
How Does SLA Work?
Most SLA printers consist of a resin vat, a build plate, a laser, and two galvanometers. The galvanometers are highly precise mirror-mounting servos, which are used to focus the laser according to the model requirements. The laser is often solid-state and has a wavelength around 405 nm. Some SLA printers have a gantry-mounted laser instead of the galvos to facilitate movement.
SLA printers utilize either the top-down or bottom-up print method. Depending on which method your printer uses, you may have to take special care when designing your model to improve the success rates of your print.
In the top-down configuration, which is more common for industrial printers than for hobby printers, the build plate is raised from the bottom of the resin vat until a small amount of resin remains on the plate. The laser is then moved or focused over the top layer of liquid resin to selectively cure a few micrometers of resin onto the plate, which is lowered incrementally into the vat for each successive layer. The process is continued to allow the layers to be printed downward until the print is complete.
In a bottom-up configuration, the build plate is lowered into the resin vat until there is a small amount of resin remaining between the plate and the membrane at the bottom of the vat. The laser is moved over the membrane to cure the resin in a pattern. The build plate is raised, which peels the cured layer off the film, and then lowered again, incrementally higher than the last layer. This process is repeated several hundred times to produce a print.
Vat polymerization: SLA, DLP, and LCD
Vat polymerization is used to refer to a few printing techniques that are often referred to in the scope of—or in comparison with—SLA printing.
Digital Light Processing (DLP) is a subset of SLA that uses a high-resolution projector rather than a laser to cure resin. Rather than point-curing with a laser, whole layers can be printed in one moment, which can improve print times drastically.
LCD Masking (MSLA) uses the same technology as DLP, except it uses a specialized LCD screen with a UV backlight instead of a projector. This method also allows for whole-layer curing, leading to lower print times than normal SLA.
One downside to DLP and MSLA technology is that unlike pure SLA, prints are “voxelized,” meaning that they are formed using 3D pixels rather than organic forms. Because of this minor difference, non-SLA prints might not capture completely organic curves and details as well as conventional SLA. For simplicity, we use “SLA” to refer to all light-curing resin printing processes mentioned.
Owing to the high-resolution printing quality and rapid speeds, SLA printing is very useful in several fields. SLA printing is excellent for printing miniatures, such as collectible figurines or tabletop gaming accessories. For industrial applications, SLA is often applied to make high-resolution prototypes. Owing to the types of materials that can be used in SLA printers, industrial applications have been extended to include medical uses as well.
Resin characteristics are manufacturer dependent. These differences can make the resin more suited for various uses, such as increased hardness or resistance. Because most resins are optimized to cure at 405 nm, it is theoretically possible to print industrial materials on consumer-grade printers. However, there are certain classes of resin that are best suited for higher-end applications than your average hobby miniature prints. We recommend starting out with a grade recommended for your printer’s intended application and only trying out the high-end resin once you have become comfortable with the SLA printing process.
Each resin will be set best under specific curing times, ambient temperatures, and build plate movement speeds. As always, starting with recommended settings and running test prints is crucial for fine-tuning these settings. Your slicer may have pre-determined settings for SLA printing, so be sure to check your printer’s profiles before changing anything drastically.
Preparing for SLA Printing
Plating the Print
First, import the model into your slicer. Many printers have their own slicers, but alternatives are available so long as they are compatible with your printer type.
Then, determine the printing orientation. At this point, it is important to be aware of where your details, overhangs, and supports are set or may be required. For resin prints, it is often best to elevate the print, rather than setting a large bottom piece on the build plate as is typical in FDM printing.
Try to orient your print to view the cross-section. This orientation can reduce the peel force stress and improve print success. Depending on whether your printer cures resin top-down or bottom-up, taper your print toward the direction your printer ends on to ensure that it is well-supported through the print.
Adding Supports
Once your print orientation is optimized, start adding supports as needed. Most slicers will auto-generate supports; however, you may wish to add your own if you find that your model is particularly prone to drooping or breaking.
Other Considerations
One major consideration when printing with resin is whether your print should be solid or hollow. While solid prints are standard in SLA, you can edit your model in Meshmixer or a similar program to produce hollow models, which require less resin and produce lighter prints. This is particularly helpful for very large resin prints that will not be subject to any force, as lighter resin prints can be much weaker.
If you do use a hollow model, it is crucial that a drainage hole is added to the model to allow resin to drain as the outside sets. It is also important to ensure that all aspects of the print are properly supported, including curves and details on the inside of the print shell.
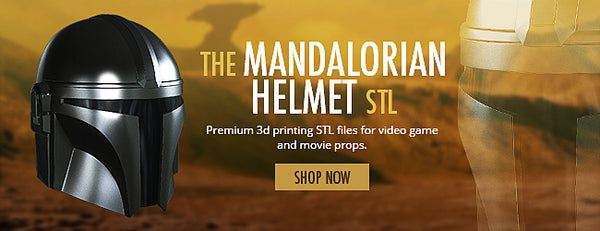
Troubleshooting
These are the common pitfalls makers experience when working with SLA that can lead to misshapen or poorly detailed prints or prints that are not easily removed from the build plate.
Resin is Too Cool
SLA printing performs best in warm temperatures. While printing with warmed resin is not necessary, it can alleviate most problems that commonly faced when working with SLA printers. Check your settings if you have a heated chamber or make your own heated chamber to keep the resin warm prior to printing.
Poor Adhesion
Similar to FDM printing, it is clear when a print is exhibiting poor adhesion as it will warp from the bed or become detached before the print is complete. There are several fixes that can address this problem:
- Re-level the bed
- Add more supports
- Use a larger brim
- Increase curing time for the base layers
- Heat the bed slightly before printing
Not enough support
If a print does not have enough supports, surfaces may be misshapen, support structures can fail, or the print can break in places. Try adding more supports or changing the print orientation to improve stability.
Problematic Resin Settings
Your resin settings might require optimization to find the perfect setup for your material. Manufacturer’s recommendations are always a good place to start but you will likely need to fine tune them.
Reset all settings to the manufacturer’s recommendations; then, try a few small test prints with different types of details and overhangs to check whether your settings require fine tuning.
Post Processing SLA Prints
After you print an object using your SLA printer, you might be in awe at how good it looks—you cannot get those details with an FDM printer. However, the print is not complete yet. After printing, the print is still “green” and requires a final wash and cure.
The washing process is simple and follows these basic steps:
- Put on nitrile (or similar) gloves and safety glasses. Extra safety equipment like a filtering mask can also be helpful. Some printers will come with a set of PPE to facilitate the post-processing stage.
- Using 99% isopropyl alcohol, submerge your part completely for at least 3 minutes. Then, swirl it around gently to remove any excess resin.
- Use a small squirt bottle filled with alcohol or a brush to remove buildups of uncured resin, which reduces residual stickiness.
You can find SLA cleaning kits on the market that include everything you need for several prints. Some makers purchase a magnetic stirring plate from laboratory companies because the minor agitation can improve the de-resining process.
While the print is still “green,” it is recommended to remove any extra supports. This can be done later, but it is easier while the resin is still somewhat soft.
After washing is complete, the print still has to be cured in full. Prints can be placed in direct sun to be cured for free but be sure to move your print throughout the curing time so that all sides are evenly exposed.
Many people have built at-home curing boxes to facilitate this process by using a dedicated UV lamp and reflective material to house the print for about five minutes. For best results, we recommend curing your SLA prints for at least half an hour. In sunlight, several hours of exposure from various angles is recommended. Because there is little risk from leaving your prints to cure for a long time, it is best to let them cure as long as you find is required for your specific print.
These guidelines are intended to be used as a reference, rather than hard and fast rules. Different resins have different characteristics and may require different cleaning solutions. In addition to our recommendations, be sure to check manufacturer recommendations for specific cleaning or curing considerations.
SLA 3D Printing Services
If you are still on the fence about diving into SLA printing or getting a new printer, you may want to see what SLA can do first. Instead of working with SLA yourself, you can send your model to a dedicated printing service and get the print shipped to you.
There are dozens of 3D printing service marketplaces online that allow you to customize your print methods and materials. Some are free to use (you only pay for the print itself) while others may charge a small premium for using the marketplace, but this can be a great way to determine whether SLA prints are a good option for the models that you want to work with.
Leave a comment